
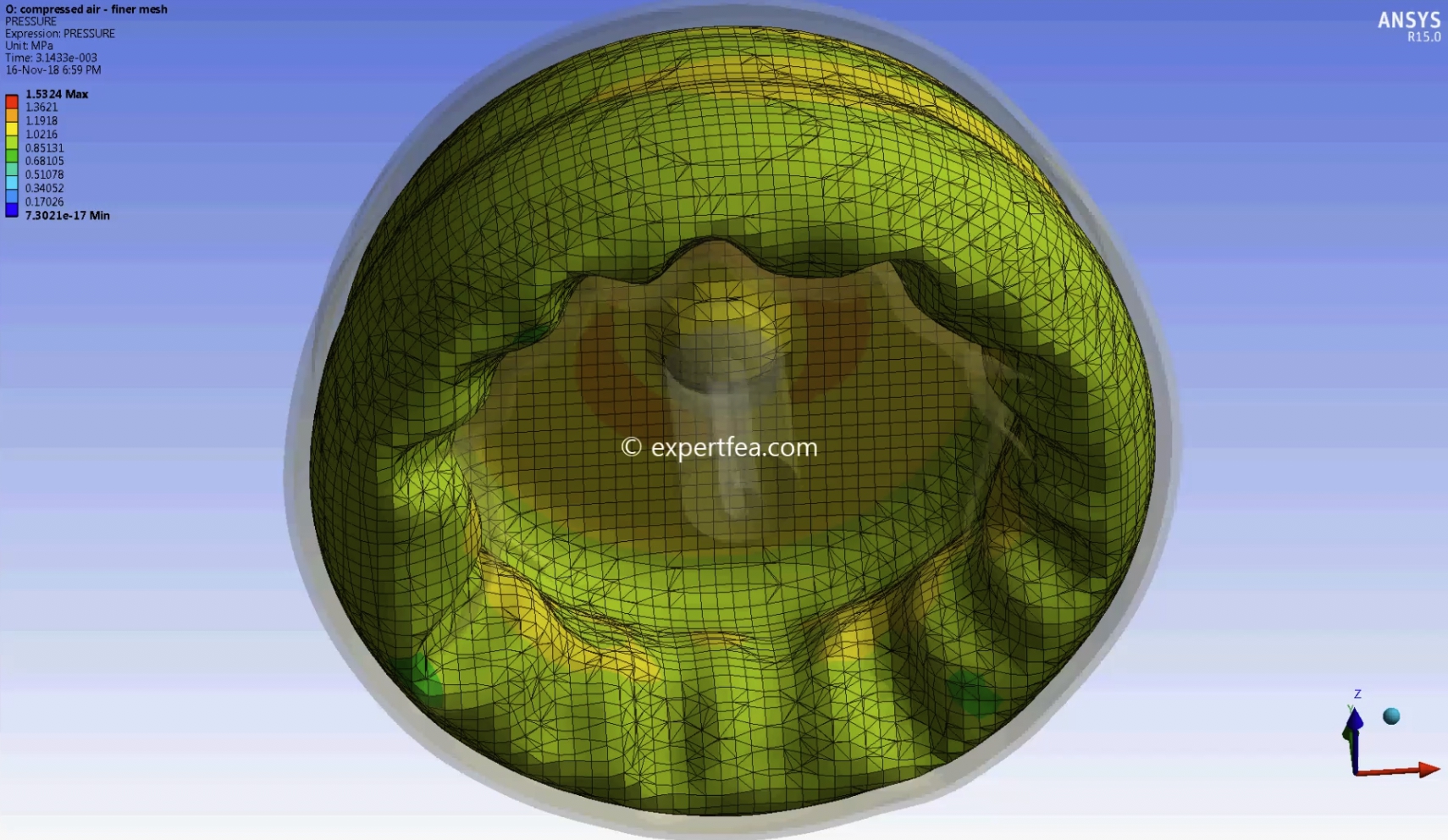
Likewise, in the same pre-processor, finite element model (mesh) that is required for computation is generated. In addition, determining and improving weak points, as well as computing life and predicting probable problems, are possible through 3D simulations in a virtual environment.ĪNSYS can import CAD data and enable building a geometry with its pre-processing capabilities. Ansys (structural and thermal) allows for more user intervention as pertaining to meshing parameters and analysis settings.īesides enabling to simulate working conditions or tests, ANSYS enables testing in a virtual environment prior to manufacturing prototypes of products.
Ansys 15 vs 16 software#
ANSYS license overviewĪNSYS is a general purpose software that is used to simulate interactions of all the disciplines of physics, vibration, fluid dynamics, structural, heat transfer as well as electromagnetic for engineers.
Ansys 15 vs 16 plus#
On another forum thread at, a forum member said Multiphysics was about $45,000 for a perpetual license plus an annual tech support fee. Ansys AutodynĪccording to one member on this forum thread, he was quoted $28,500 in the early 2000s. Use the prices inside the table below as an estimate only. We were able to find a catalog with the prices, but these prices are accurate as of 2013. On average, Athe cost of an Ansys license will depend on the number of licenses required, the nature of the license, who’s buying it and which version you want. It is capable of simulating static (stationary), dynamic (moving) as well as heat transfer (thermal) problems. It is a finite element analysis software meant for structural physics.
.jpg)
Ansys 15 vs 16 professional#
Detailed analysis of the bond formation showed, that the normal pressure distribution in the contact between wire and substrate has high impact on bond formation and distribution of welded areas in the contact area.ANSYS is a recognized market leader in FEA analysis as most professional FEA analysts prefer using it. To reduce simulation time, for the finite element simulation a restart analysis and high performance computing is utilized. The model parameters such as the coefficients of friction between bond tool and wire and between wire and substrate were determined for aluminium and copper wire in experiments with a test rig specially developed for the requirements of heavy wire bonding. Based on a co-simulation of MATLAB and ANSYS, the different physical phenomena of the wire bonding process are considered using finite element simulation for the complex plastic deformation of the wire and reduced order models for the transient dynamics of the transducer, wire, substrate and bond formation. In this contribution, a newly developed simulation tool is presented, to reduce time and costs and efficiently determine optimized process parameter. Today, process design, development, and optimization is most likely based on the knowledge of process engineers and is mainly performed by experimental testing. Many process parameters affect the bond strength, such like the bond normal force, ultrasonic power, wire material and bonding frequency. to connect electrical terminals within semiconductor modules. Ultrasonic wire bonding is a solid-state joining process, used in the electronics industry to form electrical connections, e.g.
